MENÜ
DE | EUR
DE | EUR
-
- Tischzentrifugen
- Standzentrifugen
- Gekühlte Zentrifugen
- Mikrozentrifugen
- Mehrzweckzentrifugen
- Hochgeschwindigkeitszentrifugen
- Ultrazentrifugen
- Concentrator
- IVD Produkte
- High-Speed and Ultracentrifuge Consumables
- Zentrifugenröhrchen
- Zentrifugenplatten
- Gerätemanagement
- Proben- und Informationsmanagement
Es konnten keine Ergebnisse gefunden werden.
Such-Empfehlungen
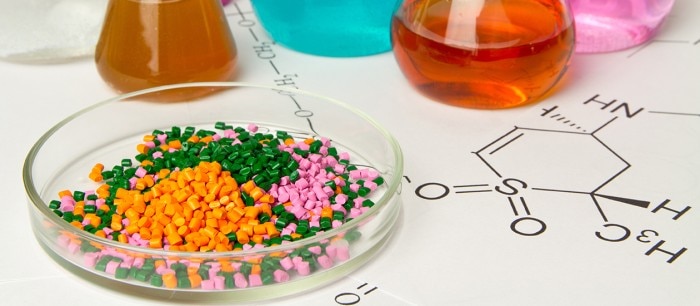
Chemical Recycling of Plastics – the Alternative to other Recycling Methods?
Dr. Kerstin Hermuth- Kleinschmidt Lab Academy
- Sustainability
- Essay
More than nine billion tons of plastics have been manufactured worldwide since the 1950s [1]. About 70% of these plastics have become waste. Most of this is due to disposable plastics – also in laboratories. Estimations show that about 5,5 million tonnes of plastic waste are generated annually from laboratory waste worldwide [2]. The question is: How can we get this problem under control and achieve a real recycling economy in which the method “Chemical recycling” can be seen as a building block in a circular economy? Let’s take a closer look at this method and the current state of the art.
How plastic is recycled today
In principle, plastics should always be recycled and brought back into a closed loop: This is the goal of a true recycling economy. The most sophisticated recycling system today is mechanical recycling for PET and PE. Many other plastics and plastic mixtures are thermally recycled – i.e. incinerated [1]. Because even the technically mature PET recycling system has its drawbacks. Only pure PET plastics can be recycled and an appropriate infrastructure for the collection of plastics is needed. Furthermore, recycled plastics do not have exactly the same material properties as virgin quality [1]. Therefore, it is not an alternative for laboratory products as these products impose strict quality criteria on the plastics used. Last but not least, the majority of plastic waste is not sorted but consists of a mixture of products that may consist either of single-sort but different plastics or are themselves made of different plastics, so-called composite plastic. These cannot be recycled by mechanical recycling, but chemical recycling could be an alternative.
Chemical recycling of plastics – a way towards circular economy?
When talking of chemical recycling one must be aware that this generic term covers several different methods [3]. In the following, we have a close look on three of them:
Solvent-based plastic recycling
Solvent-based purification works by dissolving the plastic in a specific solvent. Contaminants, additives and other impurities are removed e.g. by filtration or phase-extraction whereas the pure polymer remains in solution. In a following step, the polymer is precipitated in a second solvent in which it is insoluble. This precipitated polymer is now ready to be directly transformed into a new plastic product. So far, polyvinylchloride (PVC) and polystyrene (PS) could be recycled by this process but there are open questions regarding the fate of the solvent from the first step enriched with contaminants and additives as well as the question of solvent traces left on the output polymer [3].
Depolymerization
Depolymerization is a method suitable for certain plastics such as polyurethanes (PUR) or polylactic acid (PLA). Here, the reaction that led to the formation of the polymer chain is reversed by a suitable reaction condition. The outcome is a mixture of building blocks consisting of monomers but also dimer or oligomer fragments which could be used to produce virgin-quality polymers again [3].
Feedstock recycling
Finally, feedstock recycling is the most flexible method as it is most tolerant of the starting materials. It uses mixed plastics or composite materials as the starting material. At temperatures between 500°C-850°C, the polymer chains are broken down into smaller units and the solid plastics are converted into an oil-like liquid, the so-called pyrolysis oil. Like crude-oil this pyrolysis-oil can be used as starting material for the production of plastics. It is separated into different fractions by cracking processes in a steam cracker. The product is a gas mixture consisting of a large proportion of ethene and propene. Both can be used to synthesize polyethylene (PE) or polypropylene (PP). The polymer product does not differ from conventional PE or PP synthesized from crude oil. An alternative chemical feedstock recycling process works in the presence of oxygen at very high temperatures between 1000°C and 1200°C. This results in synthesis gas (CO, CO2, H2), which can be further converted into methanol, an important basic chemical for further downstream processes [3,4].
Is the feedstock plastic recycling process the solution for a genuine circular economy?
Feedstock recycling has several advantages which in principle makes this process a real alternative to the established mechanical plastic recycling processes. As it uses mixed waste that can otherwise only be incinerated, it saves raw materials [1,2,4]. It is insensitive towards additives whereas, in mechanical recycling, they can pose severe problems and ruin, at worst, the whole recycling process and product. Chemical plastic recycling processes do not need new infrastructure, but can use existing ones. Instead of feeding crude oil to a steam cracker, pyrolysis oil from plastic waste can be used. A study by the university of Gothenburg described the different steps of such a conversion process very detailed. The polymer product obtained from pyrolysis oil is no different from plastic products that are made from crude oil. It is therefore suitable for the manufacture of plastic products that must meet the highest quality standards. Thus, the idea of a real recycling within the framework of a circular economy is realized, since the waste can theoretically be thermally recycled over and over again, thus achieving 100% “carbon efficiency” [4]. In aside the above-mentioned advantages, chemical recycling also has some disadvantages [3,6]. First of all, this process is much more energy-intensive than mechanical plastic recycling processes due to the high working temperatures. In addition, several processes have to be linked in sequence, starting with the pyrolysis of the plastic waste, through steam cracking, to the new synthesis of the desired polymers. Environmental sustainability depends on the framework conditions, such as the use of renewable energies or the possibility of carrying out the entire process in a larger industrial cluster in order to benefit from synergy effects [4]. The economic efficiency of chemical recycling depends on various factors. These include, for example, the availability of plastic waste, which must be guaranteed at all times. This is currently a big unknown in the recycling debate, as is the risk of competition from the “power-to-liquid”-production of fuels from plastic waste [3].
Chemically recycled plastics in the lab?
Plastics used for the production of laboratory materials such as pipette tips or cell culture plates must meet very strict quality and purity criteria. For example, they must not contain any leachable components. The recycled plastics currently available on the market do not meet these quality standards, but plastics from chemical recycling do. Therefore, it could be used for high-quality plastic articles in the laboratory.
What does the future hold – conclusion and outlook
In terms of sustainability, mechanical plastic recycling is still more ecological than chemical recycling, as the latter is much more energy-intensive. A study from the Netherlands compared both processes and concluded that the carbon footprint of chemical recycling is worse than the carbon footprint of mechanical recycling [5]. Chemical recycling could therefore be seen as a supplement to mechanical recycling, but cannot and should not replace it at present. Various pilot plants all over the world are testing the technology, but there is still a considerable need for research. It may therefore take another five to fifteen years before you hold in your hands the first commercial lab product made from chemically recycled plastics – that’s how long it takes, according to current estimates, until this technology has reached market maturity [6]. Mehr erfahren
Weniger lesen
References
[1] A circular solution to Plastic Waste, Boston Consulting Group, 2019[2] Urbina, M., Watts, A. and Reardon, E. (2015). Labs should cut plastic waste too. Nature, 528(7583), pp.479-479
[3] A circular economy for plastics – Insights from research and innovation to inform policy and funding decisions – European Commission: https://www.hbm4eu.eu/wp-content/uploads/2019/03/2019_RI_Report_A-circular-economy-for-plastics.pdf
[4] Thuman, H., Vilches T. B., Seeman, M. et al. (2019). Circular use of plastics-transformation of existing petrochemical clusters into thermochemical recycling plants with 100% plastics recovery. Sustainable Materials and Technologies, 22, pp.1-35
[5] Exploration chemical recycling – extended summary: What are the opportunities for climate policy, now in the future? https://www.cedelft.eu/en/publications/2173/exploratory-study-on-chemical-recycling-update-2019
[6] eu-recycling.com/Archive/25138
Mehr erfahren
Weniger lesen
Related links
Mehr erfahren
Weniger lesen